- Change theme
What is a busbar punching machine Punching technology innovation
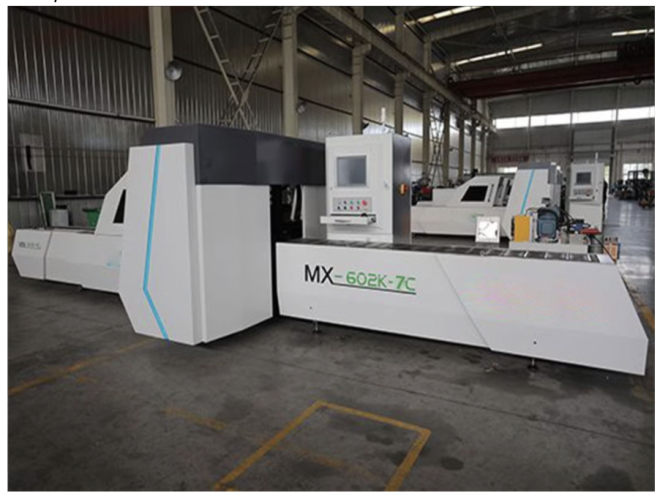
A busbar punching machine is a specialized busbar manufacturing equipment designed for punching holes in the conductive material of the busbar.
00:58 12 July 2025
What is a busbar punching machine?
A busbar punching machine is a specialized busbar manufacturing equipment designed for punching holes in the conductive material of the busbar. In the power industry, busbars play a key role in transmitting current and connecting electrical equipment, and are widely used in high and low voltage switchgear, substations, bus ducts and other scenarios. The busbar punching machine can accurately process various shapes of holes such as round and waist holes on busbars made of copper, aluminum and other materials according to different processing requirements. These holes are necessary preparations for subsequent busbar connection and installation, such as for installing electrical components and making electrical connections with other equipment. With the help of busbar processing machine, the efficiency and accuracy of busbar processing can be greatly improved, ensuring the normal operation and stable power supply of power equipment, which is of great significance to the production and construction of the power industry.
Working principle
The working process of the busbar punching machine is highly precise and orderly. The operator first fixes the busbar material to be processed on the workbench according to the design drawings and production requirements. The machine drives the die punch to apply pressure to the busbar material according to the preset trajectory and force through the control system. Under the powerful force, the punch quickly penetrates the busbar material to form the required hole position. In this process, the advanced positioning system ensures the accuracy of the punching position, so that the punched hole position can perfectly meet the design requirements. After the punching is completed, the machine will automatically stop running and the operator will take out the processed busbar. The entire punching process is efficient and fast, and can ensure the accuracy and consistency of the hole position, providing a reliable foundation for the subsequent busbar connection and installation.
Limitations of traditional busbar punching machine
(1) Insufficient precision and efficiency
Traditional busbar punching machines have obvious problems in terms of precision and efficiency. In terms of precision, due to the relatively backward mechanical structure and control system of the equipment itself, the positioning during punching is not accurate enough and is prone to deviation, resulting in errors between the punched hole position and the size and position required by the design, which cannot meet the manufacturing needs of some high-precision electrical equipment. In terms of efficiency, the punching speed of traditional punching machines is slow, and it takes a long time to complete the processing of a hole position. Frequent debugging and adjustment also further reduce production efficiency. In large-scale production, this low efficiency will lead to an extension of the production cycle, failure to meet market demand in a timely manner, increase the production cost of the enterprise, and affect the market competitiveness of high and low voltage switchgear manufacturers.
(2) Material adaptability issues
Traditional busbar punching machines have poor adaptability when facing different materials. For some busbars with high hardness or special materials, such as high-strength aluminum alloys, composite materials, etc., the punch of the traditional punching machine is easy to wear, resulting in a decrease in punching quality, and burrs and cracks may appear on the edge of the hole. For some softer materials, the punching force is difficult to control accurately, which may cause the material to deform. The different physical properties of the material, such as thermal conductivity and electrical conductivity, will also affect the punching effect, making it difficult for traditional punching machines to maintain stable performance in the processing of various materials. This limits its use in diversified material application scenarios to a certain extent.
(3) Difficult operation and maintenance
The operation of traditional busbar punching machines is relatively complicated, requiring operators to have certain professional skills and experience. During the operation, multiple parameters need to be manually adjusted, such as punching position and force, which may affect the processing quality if not carefully. In addition, the maintenance cost of traditional punching machines is high, and the equipment is prone to failure, such as hydraulic system leakage and punch wear. Maintenance requires professional technicians and a long maintenance time, which increases the production cost of the enterprise. At the same time, it is also difficult to replace parts of the equipment, and some parts may need to be specially customized, which further increases the difficulty and time cost of maintenance.
Innovation direction of punching technology
(1) Punching process
Press punching uses a press and a die to apply external force to materials such as plates, causing the material to undergo plastic deformation or separation, thereby obtaining holes of the desired shape and size. Its advantages are high processing efficiency, mass production, and the ability to achieve a variety of hole processing through different dies. Shear punching uses shear force to form holes on the material, which is suitable for processing thinner materials and has the characteristics of fast processing speed and neat hole edges. CNC punching and blanking uses a variety of dies to punch by pre-entering the processing program into the single-chip microcomputer on the CNC punching machine. The processing is flexible and convenient, with high precision and high speed, which can basically meet the needs of sample blanking production. These new punching processes have significantly improved in terms of improving precision, efficiency and material adaptability, providing more options for busbar punching.
(2) Improvement of busbar punching machine equipment design
CNC is an important direction for improvement of busbar punching machine equipment design. CNC busbar machine is equipped with a program control system that can logically process the program specified by the control code or symbolic instruction, decode it to make the punch press move and process parts, and achieve high-precision punching. The intelligent busbar punching machine realizes automated processing through an electronic control system, such as a system composed of a microcomputer control part and a photoelectric input circuit. Taking the fully automatic busbar punching machine as an example, it has a high degree of automation and is mainly used to control the processing of the window holes of the bearing cage. The intelligent punching machine has outstanding performance in automation. It can automatically complete the punching process, reduce manual operations, and improve production efficiency. At the same time, it ensures the stability of the punching quality, reduces the errors caused by human factors, and greatly improves the performance of the punching machine.
(3) Application of new materials
The application of high-strength materials in busbar punching machines can significantly improve the durability of the equipment. This type of material has higher tensile strength and compressive strength, making the parts of the busbar punching machine less likely to be damaged when subjected to large punching forces, thereby extending the service life of the equipment. The application of wear-resistant materials has a significant impact on the quality of punching. It can effectively reduce the wear of key components such as the punch, make the punching process more stable, make the edges of the punched holes smoother, reduce burrs and cracks, and thus improve the quality of punching. Moreover, due to reduced wear, the punching efficiency can also be improved, the equipment can maintain efficient operation for a longer period of time, reducing the downtime and maintenance time caused by component wear, and bringing higher economic benefits to the enterprise.
Punching Technology Innovation Case Analysis
EATON, a power equipment manufacturer, has achieved a qualitative leap in production efficiency after introducing SUNSHINE's busbar machine with a new stamping punching process. In the past, it took 10 days to produce a batch of busbar components using the traditional punching process, and about 10% of the products needed to be reworked due to precision issues. The new stamping punching process, with its efficient processing method, shortened the production cycle to 5 days and doubled the output. More importantly, the product qualification rate has increased to more than 98%, greatly reducing the waste of raw materials and labor. In terms of cost, due to the improvement in production efficiency, the energy consumption per unit product has been reduced by 30%, and the equipment maintenance cost has also been reduced by 20% due to the stability and high precision of the punching process. This series of changes has given the company more advantages in market competition, with an increasing number of orders and a significant improvement in corporate benefits.
In a large substation construction project of the State Grid Corporation of China, the CNC busbar punching machine played an important role. The project involved a huge amount of busbar processing, and the requirements for precision and construction period were extremely strict. The intelligent CNC busbar punching machine, with its advanced electronic control system, can automatically complete the complex punching process without excessive human intervention. During the project execution, the busbar punching machine worked 24 hours a day and could complete the processing of hundreds of high-precision holes per hour, greatly improving the project progress. Moreover, its high-precision punching quality ensures the stability and reliability of the busbar connection, laying a solid foundation for the safe operation of the substation. Due to the outstanding performance of the intelligent punching machine, the entire project was completed 10 days ahead of schedule, saving a lot of manpower and material costs, which was highly praised by the owner and provided a new successful example for engineering construction in the power industry.
Impact of punching technology innovation on the power industry
(1) Improving the reliability of the power system
Innovation in busbar punching technology is of great significance to improving the reliability of the power system. On the one hand, new punching processes such as laser punching can accurately control the size and shape of the hole, making the busbar connection more firm and reliable, reducing problems such as increased contact resistance caused by loose connections, and reducing the failure rate. Intelligent punching machines can monitor the punching process in real time through automated control, adjust parameters in a timely manner, avoid human errors, and ensure the punching quality of each busbar. High-quality punching reduces the heating and vibration of the busbar during operation, improves power supply stability, ensures the continuous and stable operation of the power system, allows users to enjoy a safer and more stable power supply, and lays a solid foundation for the safety and reliability of the power system.
(2) Promoting power grid construction
The improvement of punching quality has a far-reaching impact on power grid construction. In power grid construction, busbars are key components, and their punching quality is directly related to the efficiency and cost of power grid construction. High-precision punching can ensure accurate busbar connections, reduce installation and commissioning time, and speed up power grid construction. Moreover, reliable quality busbar punching can reduce the failure rate in power grid operation and reduce the workload and cost of subsequent maintenance. Punching technology innovation enables busbars to better adapt to different environments and load requirements, provide support for the expansion and upgrading of power grids, promote the development of power grids towards intelligence and efficiency, help build a more powerful and flexible power grid system, and meet the society's growing electricity demand.
(3) Cost reduction and efficiency improvement
Punching technology innovation brings many benefits to the power industry in reducing costs and increasing efficiency. From the perspective of production costs, new technologies make punching machine equipment more stable, reduce failure rates, and reduce maintenance and parts replacement costs. The application of high-strength and wear-resistant materials extends the service life of equipment and reduces depreciation costs. In terms of production efficiency, CNC and intelligent punching machines greatly increase punching speed, shorten production cycles, reduce manual operations, and reduce labor costs. New punching processes can also reduce raw material waste and improve material utilization. All of these have greatly reduced the cost of busbar processing for power companies, improved the economic benefits of companies, and enhanced their competitiveness in the market.