- Change theme
Hidden Tech in Home Appliances: Powder Metallurgy Parts
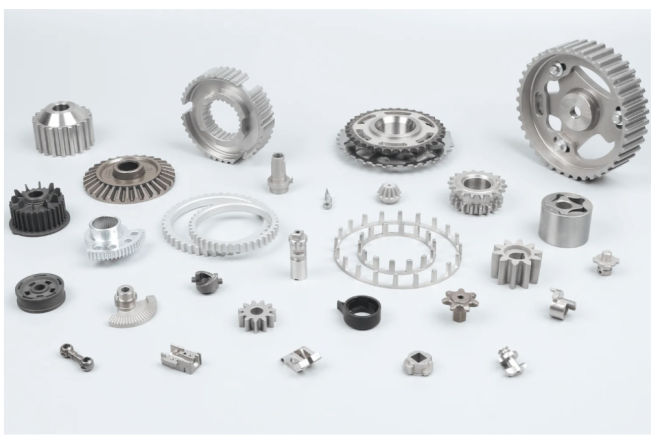
Powder metallurgy (PM) is a precision manufacturing process that forms metal parts from powdered materials.
01:59 28 May 2025
When we think of advanced technology in home appliances, we often picture touchscreens, Wi-Fi connectivity, and smart assistants. However, beyond these flashy features lies a realm of innovation that doesn’t get the same attention—yet plays a crucial role in appliance performance, durability, and energy efficiency. That hidden technology is powder metallurgy.
Powder metallurgy (PM) is a precision manufacturing process that forms metal parts from powdered materials. It enables the creation of complex components with high strength, exacting tolerances, and excellent surface finishes. While the average consumer may never see or hear about these parts, they are vital to the smooth, quiet, and long-lasting performance of everyday appliances like refrigerators, washing machines, dishwashers, microwaves, and HVAC systems.
In this article, we’ll explore how powder metallurgy is powering the invisible but essential components of modern home appliances—and why it’s the unsung hero of smart and sustainable living.
Understanding Powder Metallurgy
Powder metallurgy involves compressing metal powders into a desired shape (a "green" compact), then heating (sintering) it in a controlled atmosphere to bond the particles into a solid metal part. This process allows manufacturers to create parts that are near-net shape, meaning they require little to no finishing after sintering.
PM is especially useful for producing small, intricate parts in large volumes with consistent quality. Its advantages include:
- Minimal material waste
- Reduced energy consumption compared to traditional metal casting
- Superior mechanical properties
- Ability to produce porous or composite materials
These benefits make it ideal for parts used in appliances, where precision, efficiency, and longevity are critical.
Where Powder Metallurgy Hides in Your Home
Let’s take a tour through common home appliances and discover the hidden PM parts that make them work better, quieter, and longer.
1. Refrigerators and Freezers
Behind the scenes of your fridge’s quiet hum are several powder metallurgy components. One standout is the compressor valve plate, which is essential to the refrigeration cycle. These plates control the flow of refrigerant gas through the compressor, helping maintain the correct pressure and temperature.
Made with powder metallurgy, these plates offer high strength, excellent fatigue resistance, and precise sealing performance. This enhances the refrigerator’s energy efficiency and extends the compressor’s lifespan.
2. Washing Machines
Washing machines rely heavily on moving parts, and PM components help them operate smoothly. For example, bushings made through sintering techniques provide frictionless rotation and reduce wear.
An oil impregnated bushing—a type of self-lubricating component—is often used in the motor and drum assembly. It holds lubricant within its porous structure and releases it gradually during operation. This minimizes maintenance, reduces noise, and prevents overheating, even in high-speed spin cycles.
3. Microwave Ovens
Microwave ovens may seem like simple appliances, but their internal components are subject to frequent high-temperature use. PM parts like custom sintered gears, shielding components, and magnetic enclosures are engineered to withstand such conditions without degrading.
One such part is the sintered bushing, which supports rotating parts such as the turntable motor shaft. Its high precision and wear resistance ensure that the microwave operates silently and reliably for years.
4. Air Conditioners and HVAC Systems
HVAC systems use various powder metal parts to optimize performance. The compressor valve plate again takes center stage, as it helps regulate refrigerant flow efficiently.
In addition to valve plates, HVAC systems often include sintered filters, brackets, and structural mounts made from PM. These contribute to quieter operation, longer service life, and better airflow control.
5. Dishwashers
Dishwashers contain pumps, motors, and control arms that benefit from the strength and reliability of powder metal components. Bushings and gears made via PM reduce friction and resist corrosion from moisture and detergent exposure.
In such a demanding environment, materials created with powder metallurgy offer the ideal combination of durability, silence, and minimal maintenance.
Why Powder Metallurgy is Ideal for Appliance Manufacturers
Appliance makers face increasing pressure to deliver high-performing, energy-efficient, and durable products while controlling production costs. Powder metallurgy addresses these needs exceptionally well.
1. Precision Engineering
PM enables high-precision components with tight tolerances, essential for small motors, compressors, and actuators. The ability to design complex shapes without secondary machining saves time and cost.
2. Self-Lubrication and Maintenance-Free Operation
Parts like oil impregnated bushings significantly reduce the need for maintenance and lubrication. This is a major advantage in appliances that are expected to operate continuously or with minimal attention from users.
3. Cost Efficiency at Scale
PM is highly cost-effective for high-volume production. Once tooling is in place, large batches of consistent, reliable parts can be produced quickly, keeping appliance prices competitive.
4. Environmentally Friendly Manufacturing
Because PM generates less scrap and uses less energy than casting or machining, it supports sustainable manufacturing goals. This is particularly important in today’s eco-conscious appliance market, where energy ratings and carbon footprints matter.
Future Trends: PM in Smart and Green Appliances
As smart appliances become more common, the demand for miniaturized, high-performance components grows. Powder metallurgy is well-positioned to meet this challenge due to its ability to produce compact and multifunctional parts. Some emerging trends include:
- Smart cooling systems with compact, high-efficiency compressors using PM parts.
- Noise-optimized components in smart laundry machines for silent nighttime operation.
- Compact motors for robotic kitchen devices and vacuum cleaners with PM gears and bushings.
In the green appliance movement, where efficiency and low emissions are critical, PM will continue to be a vital part of the solution. Its role in extending the life of components, reducing friction, and conserving energy supports broader efforts to build a sustainable future.
Conclusion
Though rarely seen, powder metallurgy parts are integral to the smooth, quiet, and reliable operation of modern home appliances. Components such as the sintered bushing, oil impregnated bushing, and compressor valve plate may be hidden from view, but their impact is far-reaching.
By offering high precision, self-lubrication, material efficiency, and eco-friendly manufacturing, PM helps appliance manufacturers meet the growing demand for smarter, more durable, and more energy-efficient products.
So, the next time you load the dishwasher or hear your fridge softly hum, remember—there’s cutting-edge material science hard at work behind the scenes, all thanks to powder metallurgy.