- Change theme
Proactive Approaches to Solving Supply Chain Disruptions
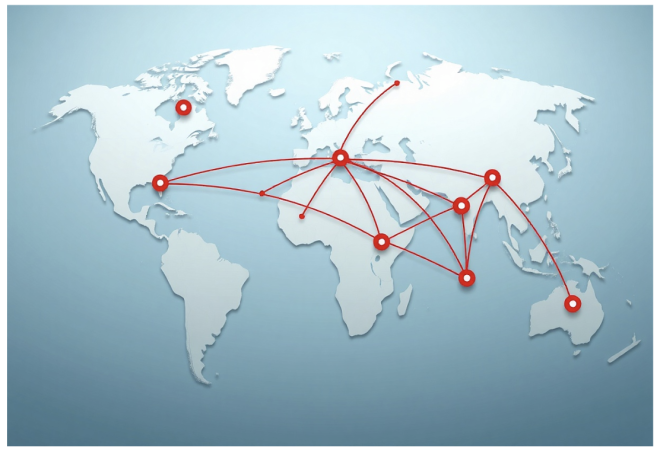
Supply chain disruptions are no longer considered an exceptional event but a reality that companies must anticipate.
00:48 03 May 2025
Supply chain disruptions are no longer considered an exceptional event but a reality that companies must anticipate. Understanding the causes and creating strategies to manage them is a key factor for success. In the following sections, we offer practical advice on how to increase a company's resilience and turn threats into opportunities—from defining supply chain disruptions to implementing tools for risk monitoring.
The predictability and stability of supply chains have become more of an exception than the rule in recent years. Companies that can quickly identify problems and respond flexibly gain a significant advantage over their competitors. Let’s take a look at the main factors that threaten supply chains and how you can recognize these threats early on.
Main Factors Causing Supply Chain Disruptions
A supply chain disruption occurs when there is an interruption or significant slowdown in the flow of materials, goods, or services within the supply system. These disruptions often have a cascading effect—problems with one supplier can paralyze the entire production process and result in significant financial losses.
The most common causes of these disruptions include:
- Geopolitical factors such as wars,
- Sanctions,
- Or regional conflicts.
These events can change the availability of crucial raw materials or components almost overnight. No less significant are natural disasters, whose frequency and intensity are increasing due to climate change.
Economic factors represent another group of risks:
- Inflation,
- Currency fluctuations,
- Or sudden changes in commodity prices.
All of this can significantly impact the cost structure. Last but not least, cyber threats are playing an increasingly important role, capable of jeopardizing even seemingly secure digital supply chain management systems.
Changes in consumer behavior and demand represent a less obvious but no less serious factor. As demonstrated by the COVID-19 pandemic, an unexpected surge in demand for certain products or, conversely, a sharp decline in demand creates significant turbulence in supply chains. This situation revealed how fragile "lean" supply strategies focused on maximum efficiency without adequate safety stocks can be.
The definition of supply chain disruption has therefore expanded in recent years—while it previously mainly covered the physical interruption of goods flow, today it must also encompass digital aspects, regulatory compliance, and reputational risks. A modern approach to this issue requires a holistic approach that includes all levels of the supply chain ecosystem.
Real-time Threat Identification
Traditional approaches to risk assessment in supply chains focused primarily on direct suppliers (tier 1). This approach is now proving to be inadequate, as a significant portion of problems arise deeper within the supply structure—with second-tier, third-tier, or even more distant suppliers.
Stay Informed
For truly effective threat identification, you should have a comprehensive overview of the entire supply chain ecosystem. Modern tools for mapping multi-tier supply chains use advanced analytical methods and artificial intelligence to uncover hidden connections and dependencies. These systems process vast amounts of data from various sources—from news articles to financial indicators—and provide real-time alerts on potential risks.
Risk Identification
A key element of these systems is their ability to identify not only direct risks but also so-called cascading effects, where a seemingly insignificant issue with a distant supplier can gradually escalate and cause a major disruption.
→ Tip: Multi-tier mapping tools provide a clear visualization of these relationships and allow you to quickly understand the potential impact of an issue, more here.
Predictive Analysis
Another important feature of these systems is predictive analysis—the early detection of signals that precede problems. Whether it's signs of financial difficulties with a supplier, geopolitical tensions in a specific region, or indicators of potential natural disasters, advanced algorithms can capture these signals and assess their relevance to a specific supply chain.
Effective monitoring is therefore not just passive tracking; its core lies in the active analysis of patterns and deviations that may signal an emerging issue. In practice, however, this requires a combination of technological tools, expertise, and adaptable processes.
Strategies for Effective Disruption Management
Early identification of problems is only half the battle—the other half is the ability to respond quickly. Addressing supply chain disruptions requires pre-established strategies that allow for flexible adaptation.
Supplier Diversification
The first principle of effective disruption risk management in supply chains is diversification. Companies dependent on a single supplier for key components are extremely vulnerable. Resilience is significantly increased by a network of alternative suppliers from different regions. This strategy requires higher coordination, but in the event of a primary supplier failure, it proves to be highly beneficial.
Strategic Inventory
Building strategic reserves of critical materials provides companies with a time cushion to adapt in case of supply chain disruptions. The modern approach is not about holding enormous "stocks of everything," but rather analyzing critical points and creating targeted reserves where the risk is highest.
Flexibility and Communication
The ability to quickly reprogram production lines or replace unavailable components with alternatives enhances adaptability. Equally important is an integrated communication system ensuring that information about potential issues is quickly shared across the entire organization.
Building Resilience
In a connected world, supply chain disruptions are not the exception but the rule. Successful companies stand out from the rest by their ability to anticipate problems and manage them effectively.
A combination of advanced technologies for mapping supplier relationships, predictive analysis, and proactive strategies form the foundation for building resilient supply chains. The true goal is not to create a chain that will never be disrupted but to build an ecosystem capable of rapid recovery.